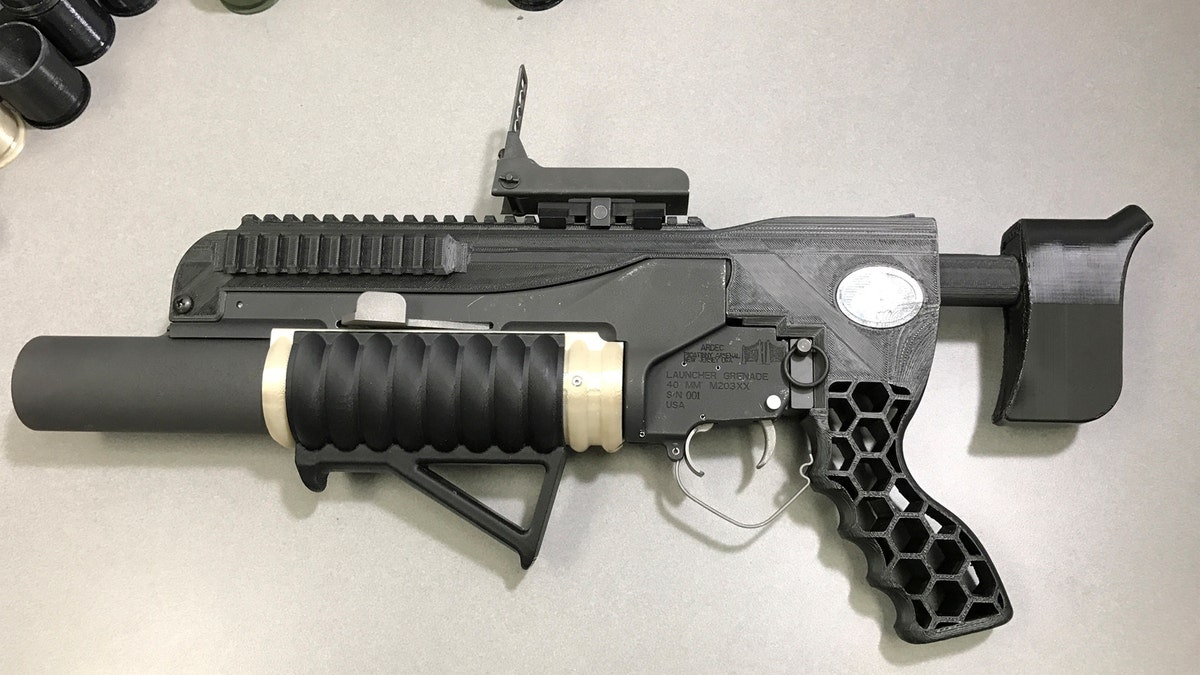
The RAMBO system (U.S. Army photo by Sunny Burns, ARDEC)
You know 3D-printing has hit the big leagues when the military starts using the technology to produce weapons. Researchers at the U.S. Army Armament Research, Development, and Engineering Center last week announced the successful development and firing of a 3D-printed grenade from a 3D-printed grenade launcher.
The grenade launcher, aptly named RAMBO (Rapid Additively Manufactured Ballistics Ordnance), was designed and developed as part of a collaborative effort between the Army Research, Development, and Engineering Command (RDECOM) and the U.S. Army Manufacturing Technology (ManTech) Program. Also involved was AmericaMakes, an accelerator program that brings together the best minds in additive manufacturing and 3D-printing technology.
The RAMBO grenade launcher is comprised of 50 parts, and all of the components, except the springs and fasteners, were produced using 3D-printing. Different parts of the grenade launcher, however, were manufactured using different materials and additive manufacturing techniques -- the barrel and receiver were fabricated from aluminum using a direct metal laser sintering (DMLS) process, while the trigger and firing pin were printed using alloy steel.
When developing the grenade launcher, the Army wanted a weapon that could move through the prototype stage and land in the hands of soldiers quickly. Instead of waiting for months for a single machined prototype weapon, Army researchers were able to 3D-print and test multiple versions of the grenade launcher in a fraction of that time. It took 70 hours to print the barrel and receiver and another 5 hours to finish off the part in post production. Overall, instead of years, it took a mere six months to produce a weapon and compatible ammunition that was suitable for test firing.
More From Digital Trends
Not only is the 3D-printing process time efficient, but it also is cost-effective from both a materials and manpower standpoint. The process of additive manufacturing can print intricate parts that would take a machinist hours to complete by hand. The 3D-printing process also can be performed autonomously, requiring an operator only to turn on the machine and check it intermittently until the process is complete. An added bonus is that no scrap material is produced during the 3D-printing process.
Besides the grenade launcher, the Army is also moving to 3D-print the ammunition for the launcher. Working at two RDECOM research and development centers, researchers were able to 3D-print a standard 40-mm M781 training round.
From a 3D-printing point of view, the grenade was a success. Three of the four main parts of the M781 grenade -- the windshield, the projectile body, and the cartridge case, were 3D-printed. Only the .38-caliber cartridge case was purchased as a separate unit and then pressed into the 3D-printed cartridge case. It is worth noting that the rounds are not live, as the addition of explosives, propellants and pyrotechnics have not been approved for use in a 3D-printed shell.
Once completed, the Army tested the RAMBO weapon using a remote firing system at both indoor ranges and outdoor testing facilities. All 3D-printed rounds were successfully fired through the launcher. Initial tests showed there was some variation in ammunition velocities, but that variance was quickly rectified by a few rounds of design changes and 3D-printing. The Army is now testing the reliability of the weapon under sustained and long-term use.